Дослідження впливу геометрії токарного інструмента та режимів обробки на процес сходження стружки
Анастасія Олексіївна Каракай
Дніпровський національний університет імені Олеся Гончара, Дніпро
Світлана Валеріївна Кицюк
Машинобудівний фаховий коледж Дніпровського національного університету імені Олеся Гончара, Дніпро
Андрій Олегович Кужиль
Машинобудівний фаховий коледж Дніпровського національного університету імені Олеся Гончара, Дніпро
Вступ
Геометричні параметри токарного різця впливають на швидкість сходження стружки, якість отриманої поверхні та інші техніко-економічні показники обробки. Фізична природа виникнення підвищення температури в зоні різання дає можливість шляхом впровадження чинників, що компенсують даний процес, регулювати його. Для цього необхідно впровадити низку заходів та умов обробки кожного конкретного матеріалу, що суттєво вплине на якість отриманої поверхні та стійкість інструменту.
Мета роботи
Дослідити вплив геометрії токарного інструмента на процес формування та сходження стружки. Визначити основні параметри, від яких залежить фізична складова процеса. Дослідити причини та наслідки підвищення, способи регулювання температури в зоні обробки.
Результати
Стружка є частиною металу, що знімається під час обробки з поверхні заготовки для отримання деталі, яка відповідає параметрам креслення.
Відповідно від параметрів зняття стружки безпосередньо залежить якість отриманої поверхні: від сил під впливом яких шар металу відділяється від поверхні, фізико-механічних властивостей матеріалу, стану оточуючого середовища особливостей технологічного процеса виготовлення деталі [1-3].
Технологічний процес виготовлення деталі характеризується застосованим обладнанням, оснащенням, інструментом, режимами обробки.
Оточуюче середовище – температура та вологість повітря в цеху, рівень вібрації на дільниці, наявність пилових забруднень, культура виробництва та інше.
Для встановлення належних умов роботи, отримання якісної продукції машинобудування, розроблені норми, нормалі, стандарти, що регламентують параметри технологічного процесу.
Вразі застосування нестандартного обладнання вищевказані нормативні документи необхідно розробити в рамках підприємства на якому експлуатується обладнання із повним дотриманням вимог державних стандартів та правил техніки безпеки.
Негативний вплив на процес обробки має підвищення температури в зоні різання в результаті дії сил, що встановлюються режимами різання (рис. 1). Основна частина тепла відводиться зі стружкою, але нагрів ріжучих кромок та передньої площини негативно впливає на результат обробки, стійкість інструменту.
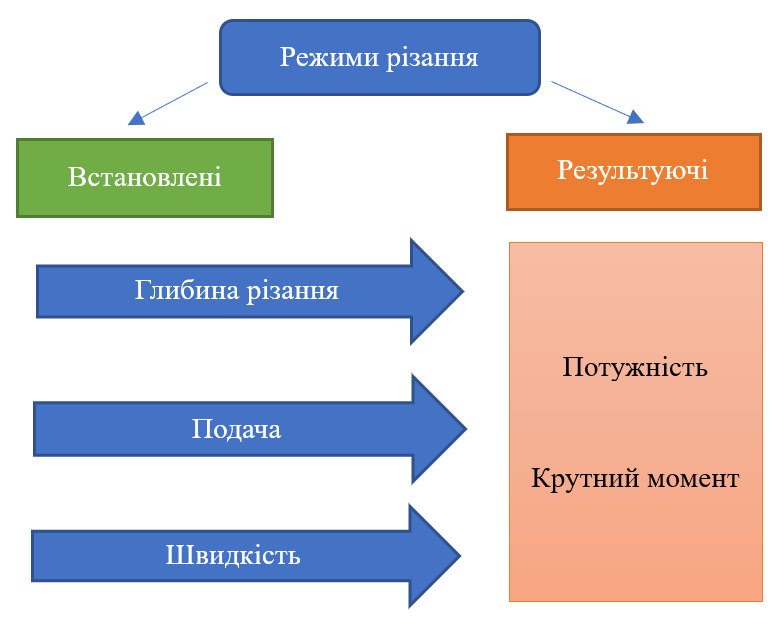
Рисунок 1 – Розподіл режимів обробки
Перший важливий чинник, що впливатиме на виділення тепла — це швидкість різання. Чим більша швидкість різання, тим більше зростає робота різання і загальна кількість тепла, що виділяється. Але найкращий ефект цього збільшення спостерігається лише при швидкості різання до 400 м/хв, а вище цього параметру вплив швидкості на температуру поступово зменшується.
Другий чинник – глибина різання і подача. При збільшені подачі температура в зоні обробки також підвищується, але не так як при збільшені швидкості різання. А ще меншого ефекту дає глибина різання, бо чим глибше ріже інструмент, тим краще умови тепловіддачі для ріжучої кромки інструмента. Для найкращого ефекту потрібно “Більше глибини і менше подачі”
І третій чинник – зміна кутів y і φ. При збільшенні переднього кута, знижується робота деформації, а отже, кількість тепла що виділяється, але одночасно с цим і погіршується умови відведення тепла. Тому спочатку температура зменшується, а при оптимальному y, починає збільшуватися. А при збільшенні кута φ тепловиділення знижується і погіршуються умови відведення тепла. В результаті чого температура різання підвищується у всьому діапазоні, де збільшили кут φ.
Отже зрозуміло, що з одного боку, велике тепловиділення допомагає легше деформувати шар матеріалу, що оброблюється, унаслідок чого зменшується знос інструменту і підвищується якість обробленої поверхні, а з іншого боку висока температура в зоні головної ріжучої кромки, яка досягає 800-1000 ̊С, призводить до погіршення ріжучих здібностей інструменту і прискорює його зношування. Крім того, нагрів інструменту і заготовки призводить зміну їх розмірів, що сильно впливає на точність обробки. Отже, тепловими явищами при різанні необхідно керувати так, щоб теплота полегшувала різання і не знижувала стійкість інструменту і точність обробки.
Вплив на температуру в зоні обробки здійснюють шляхом впровадження заглиблень на передній поверхні різця, використання змащувально-охолоджуючих рідин.
Під час автоматизації виробництва операції встановлення та зняття деталі, інструменту, виконують промислові роботи, які є машинами, працюють за чітко заданою програмою, з встановленим зворотнім зв’язком – тобто похибка встановлення при відсутності пилово-мастильних забруднень на поверхні інструменту або деталі виключена. Отже вплив на процес сходження стружки, формування поверхні деталі мають вібраційні забруднення, стан ріжучих кромок та площин інструмента, температурний режим на дільниці.
Рисунок 2 – Геометричні параметри ріжучої частини токарного різця [1]
Відведення стружки з зони обробки після відділення її ріжучою кромкою відбувається по передній площині (рис. 1). Геометричними параметрами, що формують цю площину є кути γ та λ, головний передній кут та кут нахилу передньої площини відповідно.
Рисунок 3 – Додатне (а), від’ємне (b), нульове значення кута γі [1]
Розрізняють позитивний кут λ, негативний та нульовий, що впливає на напрямок сходження стружки, на оброблену поверхню, на необроблену поверхню та перпендикулярно руху подачі.


Встановлено, що основним фактором, що впливає на величину рекомендованого переднього кута, є міцність або твердість оброблюваного матеріалу [1-4].
Умови навантаження різального леза при будь-якому методі оброблення характеризуються товщиною та шириною зрізаного шару та довжиною активної частини різальної кромки [1-4].
Висновки
Аналіз показав:
- геометричні параметри різального інструменту, їх умови, треба дотримуватись стандартам визначення;
- різці треба виготовляти так, щоб відповідали всім геометричним нормам та точності;
- технологічні бази можуть не відповідати геометричним вимогам;
- треба доцільно добирати технологічні бази для виготовлення інструмента для відповідних параметрів перетину;
- в процесі обробки рекомендовано використовувати інструмент з канавками на передній поверхні;
- обробку рекомендовано проводити з використанням змащувально-охолоджуючої рідини.
Посилання
- Паливода Ю. Є., Дячун А. Є., Лещук Р. Я. Інструментальні матеріали, режими різання, технічне нормування механічної обробки: навчально-методичний посібник. Тернопіль: Тернопільський національний технічний університет імені Івана Пулюя, 2019. 240 с.
- Алексеев Г. А., Аршинов В. А. Конструирование инструмента. Москва: Машиностроение, 1979. 384 с.
- Справочник инструментальщика под ред. Ординарцева И. А. Ленинград: Машиностроение, 1987. 845 с.