Вибір нанодисперсного модифікатора ливарних алюмінієвих сплавів
Анжела Вікторівна Давидюк
Фаховий коледж зварювання та електроніки імені Є. О. Патона, Дніпро
Вступ
Вивчення особливостей структури та властивостей алюмінієвих сплавів, оброблених дисперсними та нанодисперсними модифікаторами є актуальною проблемою матеріалознавства [1-3]. В роботі проведено аналіз існуючих модифікаторів алюмінієвих сплавів системи Al-Si, Al-Mg. На основі класичної теорії модифікування обрано типи тугоплавкого модифікатора – порошок карбіду кремнію SiC та карбіду цирконію ZrC.
Постановка задачі дослідження
Тема базувалася на відповідності кристалічних граток, комплексного модифікатора (гранецентрована кубічна гратка ГЦК) та таж сама кристалічна гратка алюмінієвої матриці. Встановлено критерії вибору нанодисперсних модифікаторів β- SiC та ZrC. Наведено технологічні параметри модифікування.
Матеріали і методи досліджень
З метою підвищення якості виливків з алюмінієвих сплавів системи Al-Si в даній роботі проведені дослідно-промислові плавки сплавів АЛ4 (АК9ч), АЛ4С, АЛ4Д. Хімічний склад досліджуваних алюмінієвих сплавів наведено в таблиці 1.
Як показано в роботах [1,3], найбільш ефективним модифікатором алюмінієвих сплавів є порошкові тугоплавкі композиції на основі карбіду SiC, карбіду ZrC до 100 нм.
Результати досліджень
Підвищення якості і властивостей виробів відповідального призначення не може бути вирішено без розробки нових і вдосконалених існуючих технологічних процесів виробництва сплавів на основі алюмінію. До відливок з алюмінієвих сплавів, що входять до складу турбонасосних агрегатів, насосів палива пред’являють вимоги, що поєднують герметичність, низьку пористість, високий комплекс механічних властивостей. При отриманні ливарних алюмінієвих сплавів важливим етапом є процес плавки і обробки розплавів. Саме на цих стадіях ефективно використовуються операції модифікування та рафінування розплавів [2, 5, 6].
Однак відсутність адаптації виливків до механічної обробки стримує широке застосування алюмінієвих сплавів як конструкційних матеріалів. Низька технологічність пояснюється наявністю в сплавах крихких і важкорозчинних фаз: FeAl3, Mg2Si, MgZn2, що виникають у вигляді великих кластерів і формують безперервну сітку. Ці крихкі фази є причиною утворення тріщин при литті злитків і фасонних виливків. Крім того, вони сприяють уповільненню дифузійних процесів розчинення інтерметалідів при гомогенізації виливків.
Розвиток сучасних технологій вимагає створення нових матеріалів і удосконалення існуючих сплавів. Одним з ефективних способів підвищення якості виливків, подрібнення зерна і отримання однорідної структури є модифікування.
Промислові підприємства застосовують модифікування ливарних алюмінієвих сплавів солями натрію, що сприяє диференціації евтектики Al-Si. Однак легкоплавкі солі натрію не екологічні і не застосовні для обробки великих мас розплавів.
Перспективним напрямком при модифікуванні є використання дисперсних тугоплавких модифікаторів: карбідів, нітридів, боридів, чистих металів з розміром частинок до 100 нм. При модифікуванні ливарних алюмінієвих сплавів дисперсними частками карбіду кремнію і карбіду цирконію розміром до від 50 до 100 нм, відзначено підвищення технологічних і механічних властивостей сплавів і корозійної стійкості [3].
В даний час існує декілька теорій модифікування, вони пояснюють певні сторони процесу модифікування алюмінієвих сплавів, але не характеризують його повністю. Це обумовлено складністю процесу і його залежністю від умов плавки і лиття, а також впливом неконтрольованих домішок і взаємодією компонентів які вводяться і які можуть як посилювати, так і послаблювати дію модифікаторів.
Всі речовини, що мають меншу електронегативність і менший ефективний іонізаційний потенціал (Uме), цим вимогам задовольняють елементи силіцій, титан, цирконій та тугоплавкі сполуки на їх основі [7].
Матеріали, що мають більше значення Uме – металевої основи сплаву, матимуть негативний вплив. Це відбувається тому, що чим нижче значення іонізаційного потенціалу, тим легше елемент віддає свої валентні електрони матриці і навпаки. Фактор, який характеризує здатність речовини впливати на процес кристалізації, слід розглядати як фактор розчинності домішок в матриці. Модифікатор повинен розташовуватися на межі кристалів і кластерів, але не входити до складу матричного сплаву.
В даний час опубліковано достатню кількість якісних робіт, присвячених модифікуванню дисперсними частками тугоплавких сполук. У дисперсних системах відображаються особливості стану поверхні, оскільки частка поверхневих атомів в дисперсних частинках є переважаючою [4]. У зв’язку з викладеним, тематика представленої роботи є актуальною для отримання якісних виливків в машинобудуванні.
З метою підвищення якості виливків з алюмінієвих сплавів системи Al-Si, в даній роботі проведені дослідно-промислові плавки сплавів АЛ4 (АК9ч), АЛ4С. Хімічний склад досліджуваних алюмінієвих сплавів наведено в таблиці 1.
Найбільш ефективним модифікатором алюмінієвих сплавів є порошкові тугоплавкі композиції на основі карбіду SiC та карбіду цирконію розміром 50… 100 нм.
Таблиця 1 – Хімічний склад ливарних алюмінієвих сплавів
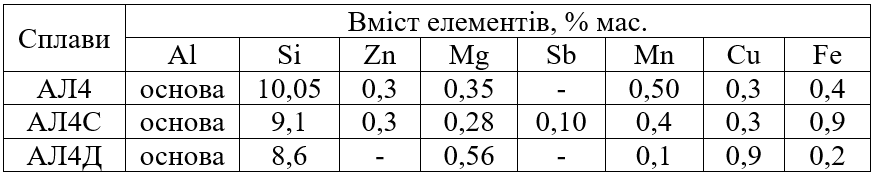
У промислових умовах були випробувані порошки комплексного модифікатора на основі карбіду кремнію, карбіду цирконію для модифікування сплавів АЛ4 (АК9ч), 2219. З метою підвищення якості та технологічності багатокомпонентних сплавів системи Al-Si поліпшення механічних властивостей проведено модифікування розплавів тонкодисперсними порошками карбіду кремнію модифікації β-SiC, ZrC розмірами від 50 до 100 нм.
Досліджувані сплави є багатокомпонентними, що призводить до можливості зміцнення твердого розчину алюмінію розчиненими легуючими елементами, а також виділенню з пересиченого твердого розчину інтерметалідних фаз, що створює ефект зміцнення при подальшому старінні. Одержуваний модифікатор є тугоплавкий карбід кремнію, карбід цирконію, який не розчиняється в розплаві, а служить додатковим центром кристалізації. Оптимальну кількість введеного модифікатора визначено експерементально на лабораторних плавках і коливається від 0,07 до 0,1% від маси розплаву.
У таблиці 2 наведені дані впливу якості модифікатора на розмір зерна.
Таблиця 2 – Вплив дисперсних добавок модифікатора β SiC на зеренну структуру сплаву АЛ4
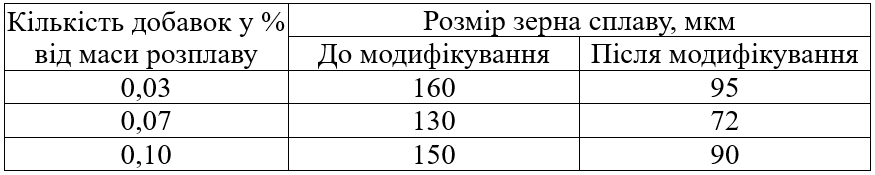
Мікроструктура сплавів у литому стані являє собою α-твердий розчин, невелика кількість евтектики і різні інтерметалідні фази, які виділяються з пересиченого твердого розчину при подальшому старінні.
В таблиці 3 наведено результати до і після модифікування.
Таблиця 3 – Межа текучості і розмір зерна алюмінієвого сплаву АЛ4 обробленого комплексним модифікатором

Проведений аналіз показав, що модифікатори карбідного класу SiC мають граніцентровану кубічну гратку відповідно до граніцентрованої кубічної гратки алюмінієвих сплавів. Це відповідає основним вимогам при виборі модифікаторів.
Експеримент свідчить, що найменше зерно (152 … 160 мкм) і найбільшу межу текучості (245 … 250 МПа) мають зразки сплаву АЛ4 у модифікованому стані.
Роботи, проведені в промислових умовах, показали підвищення механічних властивостей модифікованих ливарних алюмінієвих сплавів АЛ4 і АЛ4С до 270 МПа, що на 20% вище міцності властивостей немодифікованих сплавів.
Висновки
Проведені дослідні плавки АЛ4. Обґрунтовано вибір комплексного модифікатора на основі β-SiC та ZrC з розміром часток 50…100 нм плазмохімічного синтезу.
Основою вибору була відповідність кристалічних граток комплексного модифікатора ГЦК алюмінієвої матриці сплавів.
В результаті модифікування отримана однорідна дисперсна структура з подрібненням зерна сплавів в два рази та підвищення міцності на 20 %, що підтверджує ефект модифікування.
Посилання
- Большеков В. І., Куцова В. З. Наноматеріали і нанотехнології. Д., Пороги, 2016. 225с.
- Куцова В. З., Погребна Н. Е., Хохлова Т. С. Алюміній та сплави на його основі. Д., Пороги, 2004. 135 с.
- Калінін А. В., Грекова М. В., Давидюк А. В., Юшкевич О.П.
- Підвищення корозійної стійкості конструкційних сплавів обробкою тугоплавкими модифікаторами. Міжнародна конференція «Інноваційні технології в науці та освіті. Європейський досвід»: Матеріали у 2-х томах. Том ІІ. – Дніпро-Відень, 2017. 400 с. С. 51-55.
- Калініна Н. Є. Особливості модифікування алюмінієвих сплавів Al-Mg / Н. Є. Калініна, З. В. Вилищук // Авиационно-космические материалы и технологии. – 2011. – №7(84). – С.80-84.
- Іщенко А. Я. Зварювання сучасних конструкцій із алюмінієвих сплавів / А. Я. Іщенко, Т. М. Лабур. – Київ: Наукова думка, 2013. – 405с.
- Saunders N. CALPHAD (calculation of phase diagrams): A comprehensive guide. Oxford : Pergamon, 1998. 479 p.
- Калініна Н. Є. Модифікування високоміцних алюмінієвих сплавів дисперсними композиціями / Н. Є. Калініна // Системні технології. – 1998. – №2. – С. 150-154.