Experimental investigation of the parameters of additively manufactured coaxial swirl injectors
Samir Vekilov
Oles Honchar Dnipro National University, Dnipro
Volodymyr Lypovskyi
Oles Honchar Dnipro National University, Dnipro
Roman Marchan
FlightControl Propulsion, Dnipro
Artem Lohvynenko
FlightControl Propulsion, Dnipro
Introduction
Modern development of the intense competition on the market of Liquid Propellant Rocket Engines (LPRE) is mostly driven by occurrence of many private space companies, crowdfunding space projects, etc., which inevitably leads engineers to seeking of rational solutions with the aim of decreasing production costs along with increasing of the efficiency of the parts. Usually for successful development of the rocket engine costly equipment as well as advanced manufacturing experience is in need which explains high overall manufacturing cost.
It is due to specific requirements for individual parts that application of conventional manufacturing of LPRE is typically associated with significant time expenses, decreasing the efficiency of the production cycle. When there is a lack of necessary equipment, funds, and time, it is of high priority to find new methods of LPRE components manufacturing which do not require special tools and numerous complex technological processes, etc. Thus, it is becoming widespread to use additive manufacturing which can significantly reduce the production cycle as well as decrease production expenses [1, 2, 3].
One of the most significant components of a LPRE is a Combustion Chamber (CC) which is at the forefront of development, especially in the case of newly designed engines. In some cases, designing and production of the chamber might compose up to ~50% of the overall engine cost, and its conventional design usually is associated with significant technological difficulties [1, 2]. Thuswise, it is of high priority to use additional manufacturing for further design adaptation along with synthesis of the design solutions with unique properties [4–6].
In this work the application of additive manufacturing method for coaxial bipropellant swirl injectors production is considered. 30 coaxial bipropellant swirlers of the internal mixing were manufactured using L-PBF technology. Numerous hydraulic tests of the injectors were performed with the aim of determining its characteristics. The aim was to observe individual operation of each injector as well as collaborated work of the coaxial injectors. Spay cone angle for both individual and collaborative operation mode was of a particular interest. The obtained data is analyzed and compared to the calculated values.
Tasks and objectives
The main objectives:
- Adaptation of the design of coaxial bipropellant swirl injectors to additive manufacturing.
- Use of refractory alloy.
- Use of easily accessible material.
- Determination of coaxial bipropellant swirl injectors characteristics by carrying out hydraulic tests.
- Comparing experimental with theoretical data.
Materials and methods
The considered coaxial bipropellant swirl injectors were manufactured using relatively easily accessible material Haynes 230. The alloy is capable of withstanding high (~1149°С) and low, cryogenic temperatures, maintaining outstanding oxidation resistance, decreased thermal-expansion coefficient and great welding characteristics. As injectors are a part of a larger complex component, a mixing head which perceives a significant amount of heat flux during the engine operation, application of Haynes 230 is a rational decision.
Laser Powder Bed Fusion (L-PBF) [1, 2, 3] was chosen to be a manufactured method. Consequently, a laser beam is used to supply energy for metal powder fusion during the building process (see Figure 1).
- Let us consider a simplified procedure of the manufacturing process (see Figure 2):
- Thinking of the main design concepts and ideas.
- Developing a 3D model using Computer Aided Design (CAD) system considering technological limitations of the printer (maximum unsupported printing angle of the surface, minimal printing diameter of holes and slots, minimal wall thickness, etc.).
- Pre-printing model processing: conversion to .stl format, choice of the type and installation places of the supporting structures, etc.
- Printing process.
- Post-printing process.
Figure 1 – Laser Powder Bed Fusion process [1]
Figure 2 – Simplified procedure of the additive manufacturing process
It should be noted that currently there is no standard that regulates additive manufacturing cycle, in particular uniform quality control for produced parts. In that respect, 3D-printing parameters and post-printing procedures are often considered to be corporate property and are not subject to disclosure [2].
The objective of the hydraulic tests was to determine main characteristics of the coaxial bipropellant swirl injectors (pressure drop, spray cone angle). Each of the injectors consists of two parts: inner and outer swirl injectors (injector 1 and injector 2 respectively). The testing was performed for two regimes: individual operation of each injector and cooperative operation of both injectors. Water was chosen as a working fluid. 30 specimens were divided into 6 groups with variation of the geometrical parameters (5 specimens per group). All geometrical parameters of the injectors were normalized to nozzle diameter d (d2) of the outer injector and are represented in Table 2.
Table 1 – Geometric characteristics of manufactured injectors
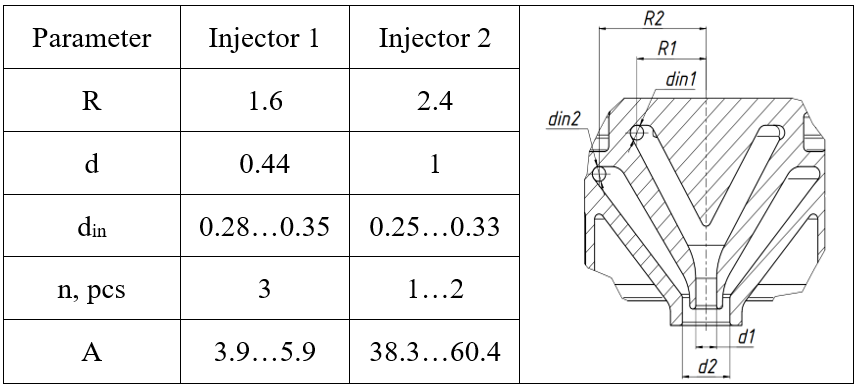
A is a geometric characteristic coefficient of the injector:

where n, pcs is a number of tangential holes; d is a normalized nozzle discharge diameter (d1, d2); din is a normalized tangential hole diameter, R is a normalized swirl diameter.
Results
According to experimental data, it is shown that between-specimen repeatability of pressure drops lies within the 5% range and is fully acceptable for engineering purposes (see Table 2). Discharge coefficient is determined following the equation:
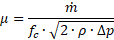
where , kg/s – mass flow rate of the working fluid through the injector; , m2 discharge nozzle cross-section; ρ, kg/m3 – density of a working fluid; Δp, Pа – injector pressure drop.
Table 2
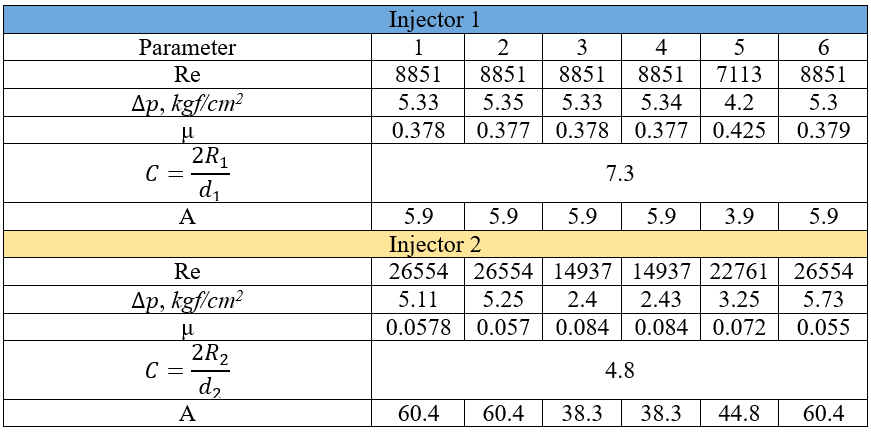
Depending on the shift of the faces of the injector’s nozzles a (see Figure 3), injectors can be divided into two groups: the one of internal and external mixing of the components. Variation of the dimension a is not considered in this work while manufactured specimens are characterized as coaxial swirl injectors of external mixing. In case of external mixing the process is typically divided into two modes: independent operation of internal and external injectors (individual spray cones do not interact, see Figure 3a) and collaborative operation mode when spray cones interact near the nozzles and result in a common, single cone (see Figure 3b). The described operation modes can also change depending on the change of the environmental density (or pressure). The exact mode cannot be determined by simple hydraulic tests. Thus, to investigate more and find the main margins of the described effect, a complex equipment for advanced research is needed and, for this reason, the effect was not considered in this work [8–15].
In terms of a spray cone angle of the conventionally manufactured swirl injectors, there are known dependencies and their margins of application. The following dependencies are considered in the review [7]. Spray cone angles of additively manufactured swirl injectors were calculated and compared with experimental data. The results are shown in Table 3.
It can be seen from the Table 3, that the known dependencies for spray cone angle assessment cannot be used in case of additively manufactured swirl injectors. The discrepancy between calculated and experimental values lay beyond even the 10% interval, which is not acceptable for engineering applications.
Figure 3 – Operational modes of coaxial swirl injectors of external mixing
Table 3 – Experimental and calculated data on spray cone angle of AM swirl injectors
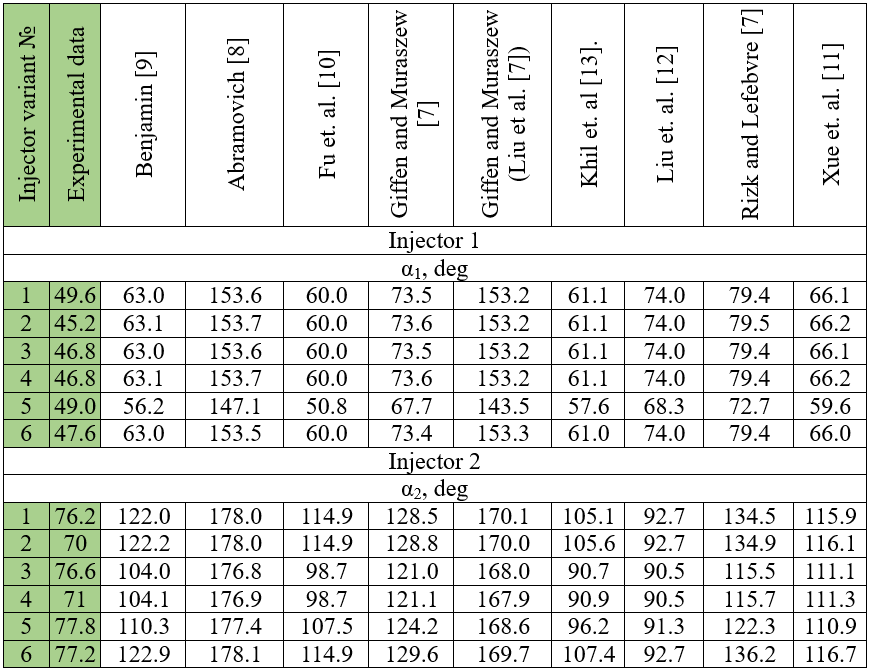
At this moment, there is no known dependency describing the resulting spray cone angle of the additively manufactured coaxial swirl injectors of external mixing. It is due to the high complexity of the process that engineers must rely only on experimental data and preliminary results for obtaining more accurate data in terms of coaxial bipropellant swirl injectors. Experimental data describing resulting spray cone angle of the studied specimens is represented in Table 4. Obtained experimental data shows that collaborative operational mode is realized for each specimen. Photos of the operation of the specimen №2 is represented in Table 5.
Table 4 – Resulted spray cone angle of the additively manufactured coaxial bipropellant swirl injectors
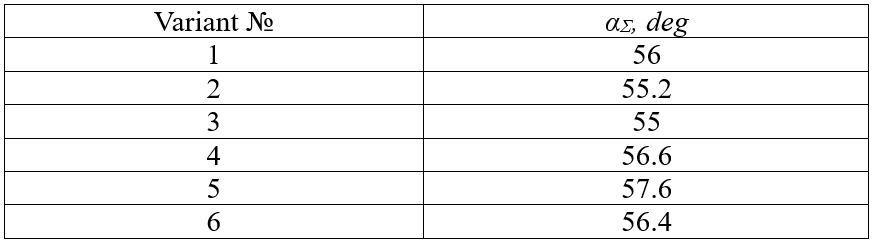
Table 5 – Hydraulic testing of the injector (variant №2)
Summary
With the purpose of investigation of the operation of additively manufactured coaxial bipropellant swirl injectors, 30 specimens were produced by L-PBF technology. As a material for injectors, a relatively easily accessible refractory alloy Haynes 230 was used. With the aim of determining the characteristics of injectors, numerous hydraulic tests were performed. According to the obtained data it found that:
- Repeatability of hydraulic characteristics of the manufactured injectors lay within 5% and is acceptable for further engineering purposes.
- Analysis of the known dependencies describing spray cone angle of the swirl injectors was carried out. The calculated values were compared to experimental data and there is a significant discrepancy between values.
- All calculated values of the spray cone angle of the individual operation mode show tendency to be larger than experimental data for each injector.
Currently there is no known dependency reliably describing the parameters of additively manufactured swirl injectors and further research is needed.
References
- Gradl P., Mireles O. Additive Manufacturing for Propulsion Component and System Applications. NASA Marchall Space Flight Center, 25 May 2021. URL: https://ntrs.nasa.gov/api/citations/20210016065/downloads/Redstone_IPT_NASA_AM-Components_Gradl-Mireles_25-May-2021.pdf
- Advancing GRCop-based Bimetallic Additive Manufacturing to Optimize Component Design and Applications for Liquid Rocket Engines / P. Gradl et al. AIAA Propulsion and Energy Forum : Virtual Event, 9–11 August 2021. URL: https://doi.org/10.2514/6.2021-3231.
- Geometric feature reproducibility for laser powder bed fusion (L-PBF) additive manufacturing with Inconel 718 / P. Gradl et al. Additive Manufacturing. 2021. Vol. 47. URL: https://doi.org/10.1016/j.addma.2021.102305.
- Distinctive features of SLM technology application for manufacturing of LPRE components / S. Vekilov et al. Journal of Rocket-Space Technology. 2021. Vol. 29, no. 4. URL: https://doi.org/10.15421/452112.
- 3D printed acoustic igniter of oxygen-kerosene mixtures for aerospace applications / R. Marchan et al. 8th European conference for aeronautics and space sciences (EUCASS) : International Conference, Madrid, 1–4 June 2019. URL: https://doi.org/10.13009/EUCASS2019-238.
- Vekilov S., Lipovskyi V. Comparison and analysis between conventional and additive manufacturing technologies of LPRE. System design and analysis of aerospace technique characteristics. 2022. Vol. 31, no. 2. P. 14–25. URL: https://doi.org/10.15421/472210.
- Review on pressure swirl injector in liquid rocket engine / Z. Kang et al. Acta Astronautica. 2018. No. 145. P. 174–198. URL: https://doi.org/10.1016/j.actaastro.2017.12.038.
- Abramovich G. N. The theory of swirl atomizers. Industrial Aerodynamics. 1944.
- Film thickness, droplet size measurements and correlation for large pressure-swirl atomizers / M. A. Benjamin et al. Gas Turbine & Aeroengine Congress & Exhibition, Stockholm, 2–5 June 1998.
- Spray characteristics of an open-end swirl injector / Q.-F. Fu et al. Atomization Sprays. 2012. Vol. 22, no. 5. P. 431–445.
- Effect of Geometric Parameters on Simplex Atomizer Performance / J. Xue et al. AIAA. 2004. Vol. 42, no. 12. P. 2408–2415. URL: https://doi.org/10.2514/1.2983.
- Experimental research on the water mist fire suppression performance in an enclosed space by changing the characteristics of nozzles / Y. Liu et al. Experimental Thermal and Fluid Science. 2014. No. 52. P. 174–181. URL: https://doi.org/10.1016/j.expthermflusci.2013.09.008.
- Quantifying the variation of the mass flow rate generated in a simplex swirl injector by pressure fluctuation / T. Khil et al. AIAA/ASME/SAE/ASEE Joint Propulsion Conference & Exhibit, Hartford, 21–23 July 2008. URL: https://doi.org/10.2514/6.2008-4849.
- Design and Testing of Liquid Propellant Injectors for Additive Manufacturing / S. Soller et al. 7th European conference for aerospace science : Materials of International conference, Milan, 3–6 June 2017.
- Effect of Inlet Slot Number on the Spray Cone Angle and Discharge Coefficient of Swirl Atomizer / M. Rashid et al. Procedia Engineering. 2012. Vol. 41. P. 1781–1786. URL: https://doi.org/10.1016/j.proeng.2012.07.383.